ECO Plant

Press Equipment
Hyundai Rotem provides the entire press process line-up on a turnkey basis based on high-speed material transfer technology and with reliable precision. All equipment in the entire process of blank production, transportation, stamping, and loading and management of final products is organically connected through automated devices to ensure the highest efficiency and productivity.
Servo Press
The servo press, which provides a next-generation press solution, is equipment that can set the optimal motion for stamping by precisely controlling the speed and position of the slide. With high-speed production of up to 20 SPM, it is contributing to improvements in product quality and productivity. It is possible to operate at low speed in the stamping section by controlling the servo motor and has the advantage of minimizing the loss of productivity and securing the best quality by mitigating the impact of contact/fracture processing. In addition, modularization of the structure and reduction of the number of parts ensure the excellent convenience in maintenance, and the noise/vibration reduction and energy-savings ensure customer satisfaction.

1200-Ton Servo transfer progressive line

1000-Ton Servo tryout press
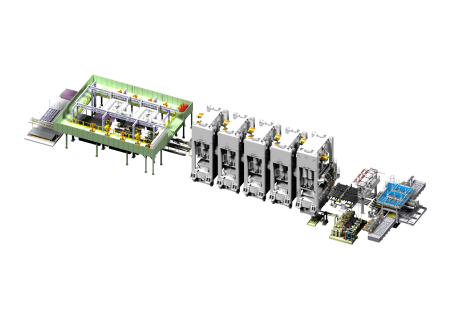
6800-Ton Servo press line
Mechanical Press
This equipment performs the entire process of warehousing of raw material, blank production, transportation, stamping, and loading and management of finished products in one-stop, thereby guaranteeing efficiency and productivity. It provides continuous automation with ease through position control between the press and the transfer device as well as productivity as high as 15~18 SPM. It uses a mechanical driving device, a main motor and a flywheel. The types include a ‘high-speed tandem press line composed of independent press equipment to improve productivity, work convenience, and stability,’ and a ‘transfer press line that operates with one drive shaft based on the interlocking operation system of the module press.’ equipped with various options such as an NC cushion system, micro inching, and a wet clutch brake, it meets the diverse needs of customers.
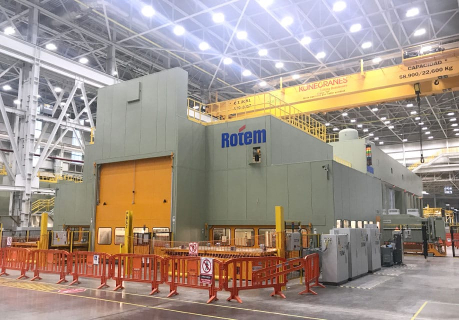
7500-Ton Tandem press line

6600-Ton Tandem press line
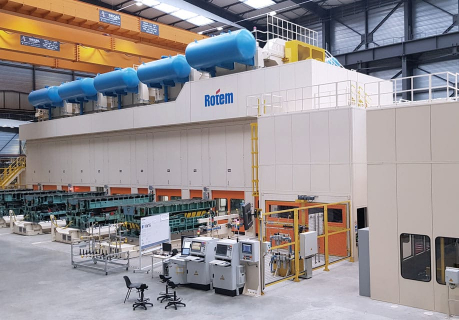
6600-Ton Tandem press line
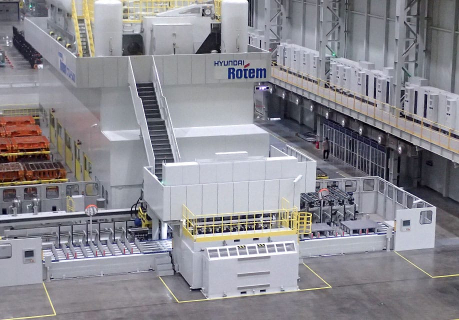
Destacker
Special Stamping Press
Special stamping Press provides a solution suitable for the user's purpose, and there are cupping, lamination, and laser blanking presses. The cupping press is high-speed press equipment for the production of beverages, food and battery cans, and provides an optimal mass production solution in conjunction with a secondary process press. The hot stamping press rapidly cools material heated to a high temperature of 900℃ or higher at the same time as press molding, enabling the production of ultra-high-strength steel sheets with remarkably high strength due to the quench-hardening effect. The lamination press is a high-speed press facility for the production of high-efficiency motor cores applied to eco-friendly vehicles. It can perform high-speed precision production of up to 300 SPM applying of dynamic balancing devices and casting frames. The laser blanking press equipment can produce blanks of various shapes by program without a mold. It has the advantages of securing flexibility in blank contour design, material savings using the CNC program freedom, no need for mold storage space, and rapid product development.

1200-Ton Hot Stamping Press line
Automation and Smart Solutions
Hyundai Rotem designs for high stability and efficiency in the metal stamping field by considering the characteristics of each piece of equipment. Each product, such as a robot, gantry system, loader/unloader, de-stacker, transfer device between processes, automatic loading device, etc., provides high productivity, safety and ease of operation. In addition, the smart maintenance system provides services that enable predictive maintenance by detecting equipment abnormalities at an early stage. These include: a coil line that automatically processes and manages all phases of adjustment and data from the receipt of the coil to the final loading of blanks after material cutting in the blanking press, a FOL (front-of-line) device that supplies material to the press line at a speed of up to 20 SPM, an automatic racking system that extracts the material that has been molded in the press line, an EOL (end-of-line) system composed of extraction conveyors, P2P as equipment that transfers materials between presses, etc.
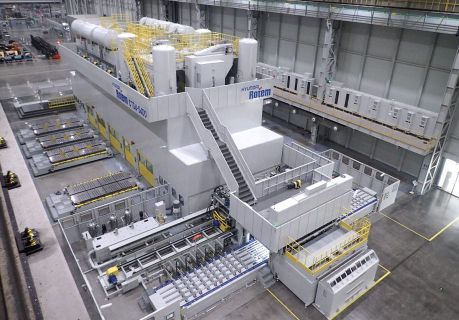
5400-Ton Transfer press line
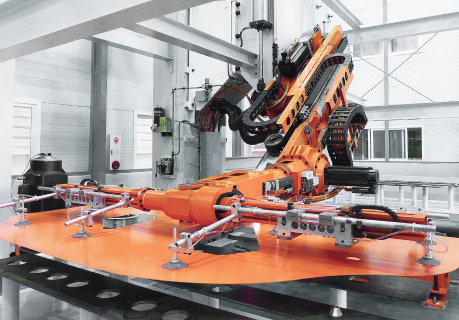
SHIFT
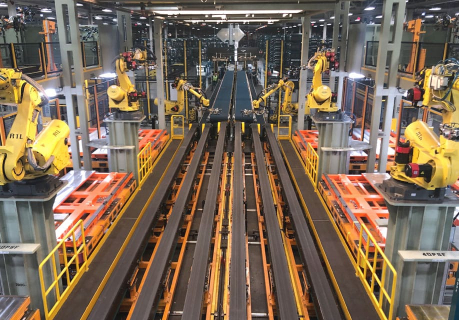
EOL Auto Racking system